Jako jedna z pierwszych osób miałem szansę zobaczyć od środka nowoczesny i bardzo zaawansowany obiekt. Mercedes-Benz Manufacturing Poland, bo o tej placówce mowa, to fabryka położona (ok. 70 kilometrów) na zachód od Wrocławia w gminie Jawor, na terenie Wałbrzyskiej Specjalnej Strefy Ekonomicznej. Cały obiekt ma ponad 50 hektarów i robi gigantyczne wrażenie. To tak, jakby w środku szczerego pola postało małe miasteczko, w którym wszystko kręci się wokół trójramiennej gwiazdy. I ciężko powiedzieć, że jest inaczej, bowiem nawet włazy kanalizacyjne mają wytłoczone logo Mercedesa.
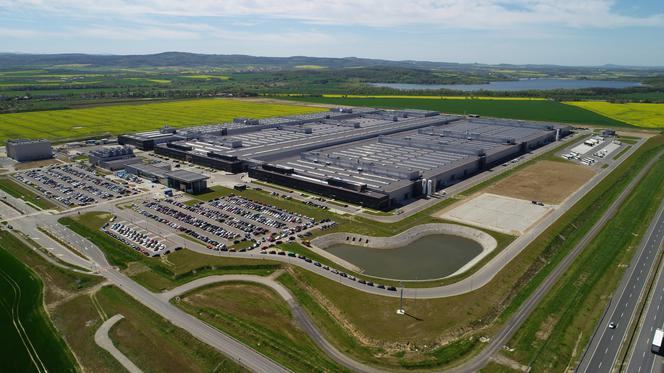
i
Powstają tu silniki i baterie
Cały obiekt składa się z kilku budynków, w których praca wrę całą dobę. W głównej hali o obszarze 20 hektarów produkowane są 4-cylindrowe silniki wysokoprężne o pojemności 2-litrów (OM654 - 195 KM i 400 Nm). Są to jednostki montowane w Klasie A, B, C i E oraz w SUV-ach GLA, GLB, GLC i GLE. W alejce obok powstają także 4-cylindrowe, 2-litrowe benzyniaki (M254 - 170 KM i 400 Nm), które producent montuje w Mercedesach Klasy C i E, a także GLC i GLE.
W hali obok, mierzącej ok. 6 hektarów, produkowane są baterie typu PB 300 (o pojemności 13,8 kWh) do niskoemisyjnych hybryd plug-in z rodziny EQ tj. Klasa C, E i S oraz GLC oraz baterie typu PB 400 (o pojemności 25,4 lub 28,6 kWh), które występują w Klasie C, E i S. Na tym jednak nie koniec, bowiem tu również powstają akumulatory typu EB 311 (68,2 kWh), do w pełni elektrycznych modeli EQA (do 426 km zasięgu) i EQB (do 485 km zasięgu).
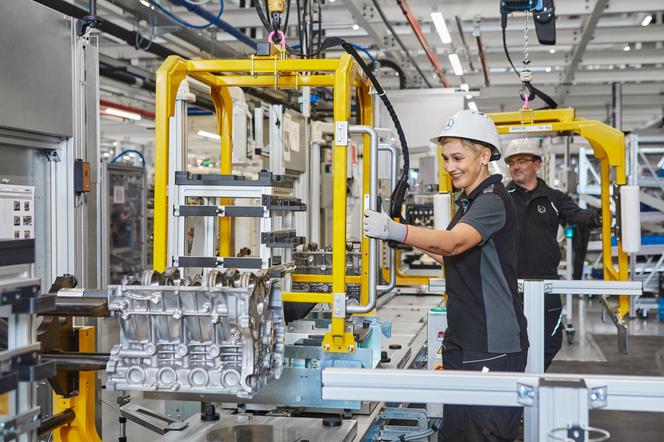
i
Jeden silnik nawet sam zbudowałem
Aby wszystko szło jak po maśle, trzeba zapewnić pracownikom najlepsze warunki do szkolenia swoich umiejętności. Świetnym przykładem jest chociażby sala edukacyjna, w której każdy może potrenować i podszkolić swoje umiejętności w zakresie budowania silników i przykręcania śrubek. Do dyspozycji pracowników jest m.in. symulator oparty o VR (Virtual Reality), czyli wirtualną rzeczywistość. W takim programie można nauczyć się jak poprawnie zamontować podzespoły do konkretnych jednostek. Osobiście sam miałem szansę wziąć wirtualne narzędzia w swoje ręce i szybko się przekonałem, że to nawet nie jest takie trudne, na jakie wygląda. Większość pracy wykonują w tej fabryce rzecz jasna maszyny, jednak przy montażu części miękkich silnika, tj. osłony czy wiązki, człowiek radzi sobie lepiej od komputera.
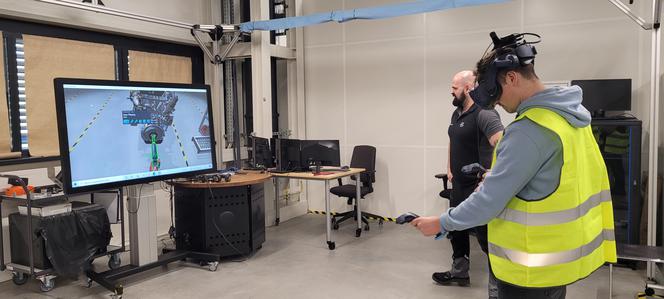
i
W zgodzie z naturą
Za całą produkcję odpowiada moment ponad 1300 pracowników, tysiące maszyn, a także autonomiczne wózki, które po halach poruszają się po wyznaczonych trasach bez niczyjej pomocy. Bez obaw, do żadnej kolizji nie dojdzie, ponieważ po wykryciu przeszkody roboty zatrzymują się w bezpiecznej odległości. Większość rzeczy, poza montowaniem podzespołów w silnikach, odbywa się automatycznie, co pozwala na wyprodukowanie rocznie ok. pół miliona silników i stu tysięcy akumulatorów. Najbardziej imponujące jest jednak to, że tak wielki obiekt jest zupełnie neutralny pod względem emisji dwutlenku węgla. Całą energię elektryczną, potrzebną fabryce w Jaworze do funkcjonowania na pełnych obrotach, zapewnia farma wiatrowa Taczalin.
Ogromna inwestycja
Zastanawialiście się kiedyś, ile kosztuje wybudowanie takiej twierdzy? Ja tak i nawet znam już odpowiedź! Suma poczynionych inwestycji wyniosła markę ponad 800 mln euro, z czego 700 mln kosztowało wybudowanie fabryki silników, a brakujące 100 mln pokryło koszt zbudowania części produkującej same baterie.
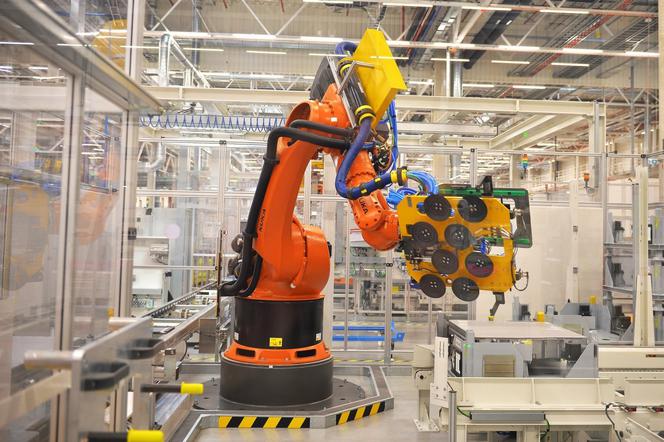
i