To ogromny zakład, pełen nowoczesnych urządzeń i technologii. Aby Elektrociepłownia działała płynnie i bezpiecznie czuwają nad nią dziesiątki doświadczonych i wykwalifikowanych pracowników.
Poznaj proces produkcji ciepła od kuchni
Wszystko zaczyna się od paliwa. Podobnie jak pozostałe zakłady cieplne Termiki, do 2035 roku EC Siekierki zostanie wyposażona w nowe jednostki, takie jak pompy ciepła i blok gazowo-parowy, dzięki którym będzie możliwe zaprzestanie korzystania z węgla. W tym jednak momencie podstawowym paliwem dla tej elektrociepłowni jest jeszcze węgiel, który dostarczany jest do zakładu głównie transportem kolejowym. Wagony rozładowuje się za pomocą specjalistycznych urządzeń, następnie węgiel trafia na plac, skąd taśmociągami przenoszony jest do młynów węglowych. W młynach jest mielony na drobny pył, następnie wdmuchiwany jest do kotłów, gdzie się spala w temperaturze 1200 stopni Celsjusza. Proces spalania wytwarza ogromne ilości ciepła i to ciepło jest wykorzystywane do produkcji energii elektrycznej, a także do podgrzewania wody krążącej w sieci ciepłowniczej, czyli tej która odpowiada za temperaturę wody w grzejnikach i w kranach w warszawskich domach, czy urzędach.
W ciągłym kontakcie
Zapotrzebowanie na energię cieplną zmienia się w zależności od pory roku, a nawet pory dnia. Dyżurny Inżynier Dyspozytorni Produkcji PGNiG Termika jest w ciągłym kontakcie z operatorem sieci przesyłowej Veolia Warszawa, z którym uzgadniany jest bieżący plany pracy oraz prognoza na kolejne dni.
Postęp technologiczny
W początkowych latach funkcjonowania zakładu praca w nim uważana była za brudną (ręczne nawęglanie) i ciężką, gdyż większość czynności wykonywało się manualnie. Teraz stosowana jest inna technika i w budowie urządzeń, i w sterowaniu. Kiedyś były klucze analogowe, dzisiaj wszystko oparte jest na systemach cyfrowych. Dużym wyzwaniem były inwestycje, które pozwoliły na przeskok technologiczny o 15 lat, oraz komputeryzacja, która znacznie zmieniła pracę na blokach.
Maszyna nie zastąpi ludzkiego doświadczenia
Wszystkie procesy zachodzące w elektrociepłowni, takie jak np. rozładunek i transport paliw, przygotowanie czystej wody, wykorzystywanej do produkcji pary, podgrzewanie i pompowanie wody, wymagają odpowiedniego nadzoru i sterowania. Proces produkcji jest w dużej mierze zautomatyzowany, jednak nad wszystkim czuwają doświadczeni pracownicy. Kliknięcie myszką powoduje, że ogromne urządzenia wprawiane są w ruch. Tysiące ton paliwa bez konieczności użycia siły fizycznej trafiają do kotłów. Szczególnym miejscem w takiej elektrociepłowni są nastawnie. Znajdują się tam dziesiątki komputerów – to swoiste centra dowodzenia, które działają 24 godziny na dobę. Operatorzy nastawni otrzymują setki sygnałów z nadzorowanych urządzeń, monitorują parametry i szybko reagują na zmiany. Ich praca wymaga skupienia i szczególnej czujności. W przypadku zakłóceń potrafią bardzo szybko zareagować i poprowadzić instalację w sposób gwarantujący dotrzymanie parametrów produkcyjnych.
Cały proces produkcji jest niezwykle skomplikowany. Pracownicy przechodzą długie szkolenia zakończone egzaminami, po których nadawane są im uprawnienia do obsługi różnych urządzeń. Nowo zatrudnione osoby są wdrażane przez doświadczonych kolegów, którzy dzielą się swoją wiedzą i wskazówkami. Doświadczenie i znajomość urządzeń produkcyjnych mają tu szczególną wartość.
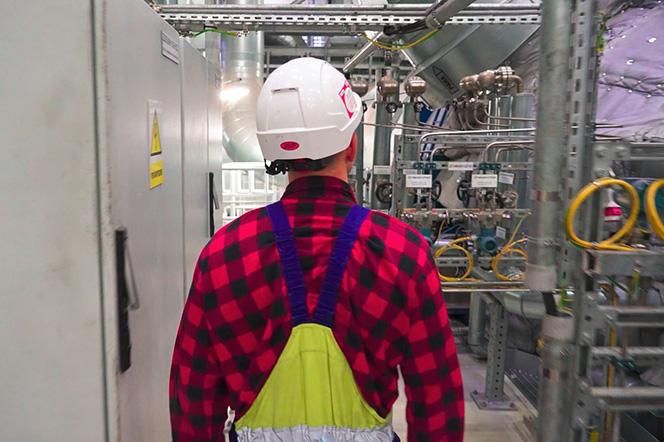
i
Szybka reakcja na zapotrzebowanie na prąd
EC Siekierki produkuje nie tylko ciepło, ale i prąd. Podobnie EC Żerań, gdzie nowoczesny blok gazowo-parowy (BGP) stanowi ważny element warszawskiego węzła systemu elektroenergetycznego. W 2021 r. zastąpił urządzenia, na których od lat 50-tych opierała się produkcja EC Żerań, pozwalając na generację niemalże 500 MWe. Jego zaletą jest znaczna elastyczność pracy, uwzględniająca krótki czas uruchomienia oraz zmienność obciążenia w zależności od bieżących potrzeb KSE (Krajowego Systemu Elektroenergetycznego). Mimo ogromu urządzeń składających się na BGP, całość sterowania skupiona jest w nastawni, skąd pracownicy sprawują nadzór nad pracą jednostki, w tym produkcją ciepła, energii elektrycznej oraz pary technologicznej.
Niebezpieczna praca
Obcowanie z paliwami oraz skomplikowanymi urządzeniami niesie za sobą ryzyko niebezpiecznych zdarzeń, dlatego Termika regularnie przeprowadza ćwiczenia obejmujące takie scenariusze, jak symulowany pożar czy rozszczelnienie instalacji. Pozwala to potwierdzić sprawność systemów bezpieczeństwa oraz zapoznać jednostki Straży Pożarnej z topografią i urządzeniami zainstalowanymi w zakładach oraz potencjalnymi zagrożeniami przy nich występującymi.
Misja i odpowiedzialność
Zakłady Termiki działają w trybie „24/7”, co oznacza, że czasem pracownicy muszą spędzić w pracy również święta. Podchodzą do tego z ogromnym poczuciem odpowiedzialności. Wiedzą, że to, co robią, ma znaczenie – że to dzięki ich pracy tysiące ludzi w Warszawie mają ciepło w kaloryferach, gorącą wodę do kąpieli i prąd w mieszkaniach.
Partnerem materiału jest PGNiG TERMIKA S.A.